I was born in Newcastle-upon-Tyne, England, and educated in Chicago, IL. I received my BFA from the Center for
Creative Studies in Detroit, MI in 2000, and my MFA from Cranbrook Art Academy in Bloomfield Hills, MI in 2002.
With a chemist for a father, I grew up fascinated by transformations in nature. Through the forging process
elemental inorganic steel takes on some qualities of the organic. The pattern welded vessel series started off as
an experiment to see how far one could stretch a block of layered steel before it began to de-laminate; so there
has never been an ideal combination of metals that I have used in these pieces. As a metalsmith, I try to use the
entire vocabulary of materials available to me to enhance the piece. My metal work has its foundations in both
ferrous and non ferrous metals and has resulted in objects ranging from full scale architectural pieces to
sculpture, to mechanical jewelry, to a range of Western/Japanese weapons. I enjoy the juxtaposition of old
technique and new materials or processes. This relationship makes for pieces that take a new look at
time-honored endeavors in metalsmithing. I often wonder what the world of metalsmithing would look like if
the craftsmen of antiquity had the technology of today.
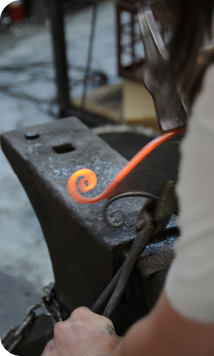
I have always appreciated the interaction between jewelry and wearer. From day to day ornamentation,
to one's finest formal jewelry, the act of adorning one's self is a ritual. Personal ornament changes the
wearer as it creates a moment when setting an intention can be as effective as turning a dial or flipping
a switch. This change in frequency can be simple; from public face to private face, to protection, to
empowerment, jewelry allows us to alter ourselves through a seemingly mundane act. We routinely use
this behavioral mechanism to create a moment that signifies a change or permanence in ourselves.
As the crusaders made their way through the middle east, they came across a new
kind of iron weapon: the damascus blade. Named for the city of origin, these
weapons were comprised of two kinds of steel folded together. At the time, this
was the best way to ensure a homogenous metal with even properties throughout.
Two steels with different carbon contents were forge welded together, cut,
re-stacked, and forge welded again and again. The result was a pattern of layers
in the steel. All damascus steel shown on our website has been created in the
forges at Burdett Metalsmithing and Design.
Mokume Gane, translated is wood grain metal, is a laminating or diffusion process
developed by the ancient Japanese. The process is very similar to Damascus making
except it is done with non-ferrous metals (metals not alloyed with iron). In this
process, layers of alternating gold, copper, brass, silver, or nickel silver are stacked
and clamped together under high pressure. The stack is then heated to a
semi-liquidius state. As the two metals develop a skin of almost molten metal, they
begin to alloy, or melt into one another, creating a permanent bond. The stack,
once fused or laminated is then called a billet. From here, the material can be
formed into bar or sheet. During the forming process, material is removed via
grinding, chiseling, or drilling to expose layers within the billet. As the material
becomes thinner, the exposed layers come to the surface creating pattern.
Mokume gane was traditionally used for sword guards and decorative vessels. As
the patterning process is so tightly controlled, it can be very detailed, or specific
as to depict an animal, show letters and words, images, etc. All Mokume Gane
shown on our website has been created at Burdett Metalsmithing and Design.